PROBLEM SOLVING IN SUPPLY CHAIN PROCESSES
Modern supply chains are identified by a high degree of complexity, which may be divided into some fundamental aspects:
- articulated production and distribution processes;
- characteristic parameters subject to variability;
- risks of various kinds;
- physical, procedural or conceptual constraints;
- changing behavior of system variables over time.
In general we can state that the processes of Supply Chain Management (SCM) field, such as planning, production, logistics, transportation and so on entail data-driven decision-making situations. Data must be appropriately collected and organized in databases to be subsequently converted into useful information through processing and visualization tools.
However, “traditional” data processing (for example by exploiting reports) may not be sufficient to support the decision-making process: the consequences deriving from a decision have in fact a systemic effect on many other company areas.
Understanding the effects on different company performances then becames simultaneousluy necessary and onerous.
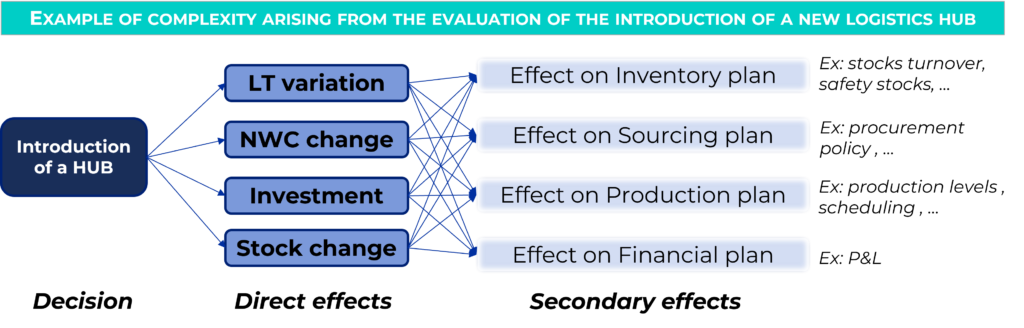
Choosing the right approach to represent and manage supply chain complexity can therefore prove to be a decisive factor for the decision-making effectiveness of SCM processes.
Among the most commonly used and recognized methods for evaluating the effects of a decision there are: analytical methods and dynamic simulation. Let’s analyze them briefly.
Analytical Methods
Analytical methods represent the problem as a model of equations which include the variables to be optimized. These equations are solved using some solving algorithms such as, for example, CPLEX. Equations cannot be excessively complex: for this reason the constraints and variables of a given problem (which are deterministic and non-stochastic in nature) must be simplified and standardized as much as possible.
The time interval considered is an integer, discretized dimension (subject to the so called bucketing) and the events are static.
The analytical method provides the decision maker with a black box view of the model’s solutions: there is visibility only on the input and output data, while understanding how a certain result was obtained may not be simple or intuitive.
Finally, when optimizing the parameters considered, a predefined set of objectives is normally considered, typically of an economic nature.
Dynamic Simulation
In the case of simulation, the problem considered is modeled at user’s discretion, through a series of entities that interact with each other through cause-effect relationships. The model obtained describes, over time, how the entities behave and what types of interactions they will establish with a very high level of detail (e.g. individual operators).
In this case time, unlike the analytical method, is represented as a continuous dimension.
The simulation process does not have the task of optimizing any variable: on the contrary, it allows the user to understand the dynamics that regulate the model and verifies the performance based on the hypotheses provided, commonly called scenarios.
Choosing the right method for supporting decision making
Which method should then be used to make the decision-making process effective?
There is no single answer: any tool, whether dictated by experience, an electronic spreadsheet, an analytical method or
simulation, can be more or less useful for the purpose. However, you can think of using two metrics to evaluate the choice of the most suitable tool: speed of problem resolution and precision of the result achieved.
The first concerns the time necessary to logically formulate the problem and to find the solution, while the second concerns the reliability of the results obtained and the ability of the tool to report the complexity of what is being considered.
It is possible to briefly present the main problem solving tools as shown below, with their relative advantages and disadvantages linked to their use.
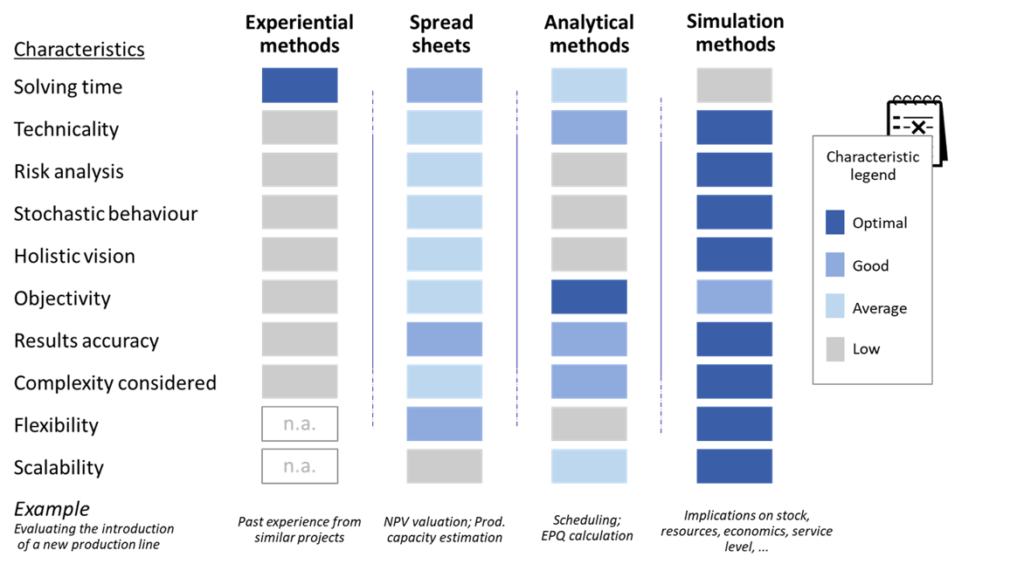
The choice between a simulation-based method and an analytical method is not exclusive: in some cases, using both tools combined allows you to achieve the best results.
One could think of analyzing a decision using an analytical approach and then developing alternative scenarios using simulation or vice versa, generating sub-optimal scenarios for a given problem through simulation and then moving on choosing the optimal scenario using an analytical method .
Some typical decisions of SCM processes that find valid decision support in simulation may concern:
- Design (or re-design) of the supply chain: if the value chain presents systematic inefficiencies, it is necessary to intervene on the variables of the logistics network to ensure the correct level of service and cost efficiency. For example, the repositioning of storage or production sites can be one of the typical decisions made in this context. In this case the simulation can help to develop a Network Redesign that provides valid alternatives for the positioning of the sites, both at a geographical, operational capacity and economic level. The input data considered by the model will therefore concern the current location of the facilities, their storage capacity, production capacity and the reduction/increase in fixed and variable costs. As an output, the model will allow to verify in detail how the level of service, the structure of costs and revenues as well as any environmental impact vary depending on the different scenarios hypothesized for the new distribution network.
- Product portfolio review: the simulation approach is particularly useful for evaluating the introduction or removal of SKUs in the market. An analysis of this type allows to verify the saturation of production and storage capacity, the effectiveness in responding to market needs and the possibility of cannibalization of existing products.
- Long-term production planning: based on the sales plans agreed with the commercial function, it is possible to simulate various scenarios for verifying the saturation of production capacity to anticipate any critical issues in the medium-long term. This results in decisions to modulate the production capacity of the plants in order to adapt it to events expected in the future, such as: seasonal peaks, new market trends, changes in market share, promotions, etc.
- Review of inventory policies: it is a decision-making situation that is taken by mutual agreement between the production function and the sales function, when there are important changes in the structure of the supply chain, in the demand presentation patterns or in financial targets for reducing working capital. In this case it may be necessary to review the parameters for managing stocks of finished products, semi-finished products and/or raw materials to accommodate the new objectives. In this decision-making situation, simulation allows you to carry out a sensitivity analysis on the management parameters of the inventory policies (such as: reorder point, reorder quantity, safety stock, maximum stock, etc.), quickly identifying the optimal values through the comparative analysis of different scenarios.
In conclusion, at different moments in time companies are called upon to make a certain number of strategic decisions of different importance, relevance and complexity. It is therefore possible to group decisions according to the convenience of using analytical rather than simulation methods, as shown in the figure.
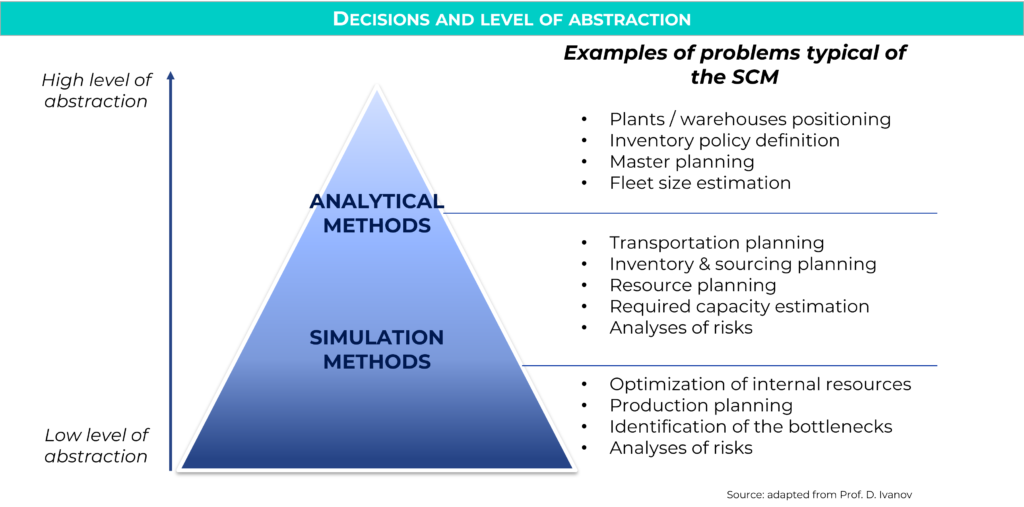
01
Problem solving in supply chain processes
Problem by problem: Analytical methods and Dynamic Simulation compared
02
Dynamic simulation as decision support
How to choose the right simulation methodology for a tailor made approach to reliable data-driven decision
04
Skills and technologies
Learn about the skills and technologies involved in this cutting-edge technology
06
Applying Simulation to the S&OP process
MRP, Scheduling, and in between Simulation Modelling: discover how